A Closer Look at Frequent Inspection Points for Overhead Cranes
- By websitebuilder
- •
- 08 Dec, 2017
- •
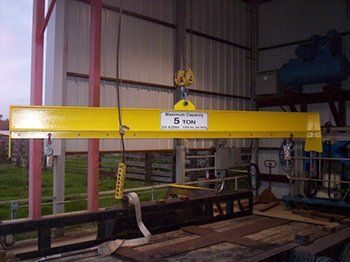
Whether you own a small construction business that uses an overhead crane or you have a massive operation that involves the use of several cranes, proper inspection is vital to the safety of your employees and the well-being of the equipment itself.
The Occupational Safety and Health Administration defines two different types of crane inspections: frequent inspections and periodic inspections. While periodic testing should be performed in 1 to 12-month intervals, frequent inspections should be done in daily to monthly intervals. Most crane owners and operators opt for daily inspections before the start of every shift just to be safe.
Here is a closer look at the details of the frequent crane inspection so you are prepared for this process as a crane owner.
Inspection of the Air Hydraulic System
The air hydraulic system is the powerhouse of the overhead crane, and it is also where mechanical problems can first show up. There are several points of the air hydraulic system that should be inspected frequently, including the:
- Drain pumps
- Valves
- Hoses
- Fluid reservoirs
These components must be checked carefully for signs of wear and tear, and for signs of deterioration and leaks of hydraulic fluid. Any other operational component of the hydraulic system should be included in the inspection.
Inspection of Hooks
The hooks of an overhead crane are some of the smaller components of the overall setup, but they do the heavy lifting, as they pick up the item to be hoisted, so the hooks must be regularly assessed. If you spot any problems with a hook, whether it is a small crack or slight bend, the crane should be shut down and the hook should be replaced.
Inspection of Functional Mechanisms
Your frequent overhead crane inspection should include visual surveying of the functional mechanisms for maladjustments and regular wear and tear. Functional mechanisms of an overhead crane are components like the bridge girder, limit switch and wheel assembly.
Maladjustments of these functional mechanisms are problems in the overall adjustment of the crane, such as a wheel assembly that is not properly seated. Regular wear and tear of the functional mechanisms would be issues like a worn bridge girder.
Inspection of Hoist Chains
While the hydraulic system does the heavy lifting, the hoist chains must support the heft of the item being lifted. Therefore, frequent inspections of the hoist chains of an overhead crane are a must. There are several forms of wear and tear that can occur with regular use of a hoist chain, and each should be immediately addressed. Some examples of wear and tear to the hoist chains include:
- Twisted end connections
- Excessive wear of chain links
- Overstretching of chain links
- Distorted links or end connections
Each of these occurrences of regular wear of a hoist chain can prevent the hoist from fully supporting the load as it should. This can cause a dangerous situation if not caught before a lift is performed with the overhead crane.
Inspection of Rope Reeving
Rope reeving refers to the metal rope that is used on many overhead cranes in place of a chain. Before every operating shift, the rope reeving should be examined for proper placement and wrapping around its drum coil. You can find information for proper rope reeving in your manufacturer-provided owner's manual.
Even though frequent crane inspections can seem to interrupt workflow and slow you down, inspections increase the safety of the equipment and lower risks to the people working with the equipment. It is during these inspections that safety hazards or problematic components are caught before they create a huge problem. There are good reasons for these inspections.
For more information about crane inspection, contact us at Advanced Crane Services for help.
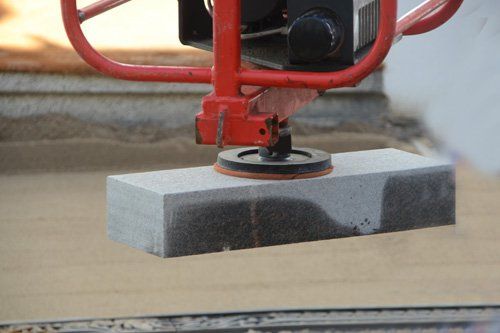
At many construction sites, contractors and workers commonly use conventional load-lifting equipment, such as hoists and chains. While this equipment does get the job done, workers face increased safety risks when handling material using manual lifting attachments.
Vacuum lifters offer a better solution for contractors who want to improve safety and efficiency at worksites that require the handling and lifting of heavy loads.
Read on to learn more about vacuum lifting and the benefits of choosing this technology over traditional lifting methods.
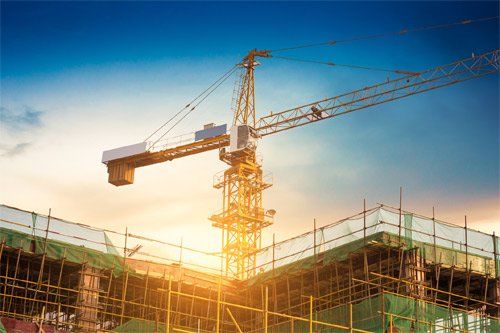
Cranes are an essential piece of equipment on job sites in a vast range of industries, from high-rise construction to product fabrication. When your crane functions properly, this machine can be one of the biggest assets at your worksite due to its load-bearing capacity and task versatility.
However, when crane issues arise, these problems can have serious repercussions. Cranes can be some of the largest and most relied-on pieces of equipment on commercial and industrial worksites, and a breakdown can lead to profit loss, delays, property damage, safety hazards, and even injuries.
Some crane issues your employees may notice during point inspections or normal operation can be addressed by a scheduled service call or through routine maintenance. However, other problems require immediate response, often through emergency repair services.
In this blog, we help you identify when your crane requires emergency services versus routine repairs.
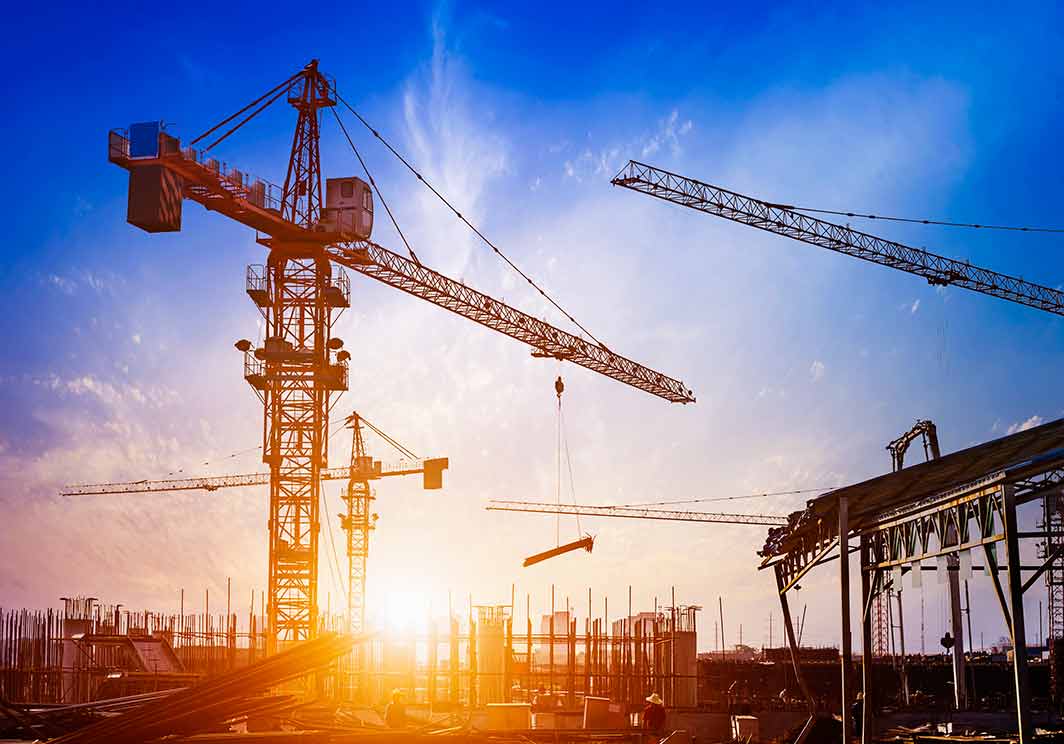
Cranes are an essential piece of many construction, fabrication, mining, and other industrial job sites. When your crane no longer performs as it should, your business productivity and worker safety can suffer. In this situation, you must decide on the best solution to get your production or building project back on track.
For many business owners, the decision for resolving the issue of worn out lifting equipment comes down to either crane modernization
or replacement. Both options are a significant investment in the future and function of your business, and you obviously want to choose the right solution.
In some cases, crane modernization is significantly more cost-effective than full replacement. In this blog, we explain the basics of the modernization process and the factors that may make this option right for your business.
What Is Crane Modernization?
Crane replacement obviously involves disposing of your current machinery and investing in a new piece of heavy equipment. Crane modernization involves selective replacement to retain the intact portions of your existing crane and eliminate any damaged, worn out, or non-compliant components.
Common modernized parts include:
- Bearings
- Brake systems
- Controls
- Drive systems
- Gears
- Wheels
Crane modernization is a frequently used solution in numerous industries because crane structures can last for decades, while individual systems can wear out much more quickly. Crane modernization can also introduce new technology into older modern cranes to create a more efficient result out of what was originally an outdated model.
When Is Crane Modernization a Viable Option?
Because crane modernization only requires your crane expert to work with portions of the machinery, this solution is more affordable than full replacement. However, cost is not the only factor you should consider when making this decision since modernization is not a cure-all for crane problems.
Crane modernization tends to be most viable in situations where small repairs are no longer enough, but the majority of the crane's structure retains its integrity. Your crane may be a good candidate for modernization if it:
- Has caused any employee injuries due to malfunctions or inadequate performance
- Has outdated hoist systems
- Needs a higher loadbearing capacity
- Needs frequent repairs to retain a satisfactory performance level
- Needs a new drive system due to system failure or low system performance compared to newer technology
- No longer meets industry requirements due to equipment age or regulation changes
- No longer meets OSHA safety standards such as loadbearing ratings
- Numerous parts are no longer under warranty
- Requires a power source change, such as a switch from DC to AC current
- Will be used for other applications in the near future
Modernization can also be particularly useful when your crane is an older model and repair workers have trouble finding replacement parts or these parts have become abnormally expensive due to being outmoded. Upgrading the technology should result in fewer repairs and cheaper replacement components in the future.
One of the first steps in determining whether or not you should consider crane modernization is to have a full inspection performed, including load testing. If your crane falls short on safety or performance and/or exhibits any of the characteristics listed above, you should consider modernization as a way to get your equipment back on par.
If you think that modernization may be the ideal solution to return your crane to its optimal operating performance, schedule an inspection and estimate as soon as possible. If you still feel unsure about how these options may apply in your specific situation, discuss your options with a crane maintenance expert.
For expert crane work, trust the experienced team at Advanced Overhead Crane Services. We're ready to help.
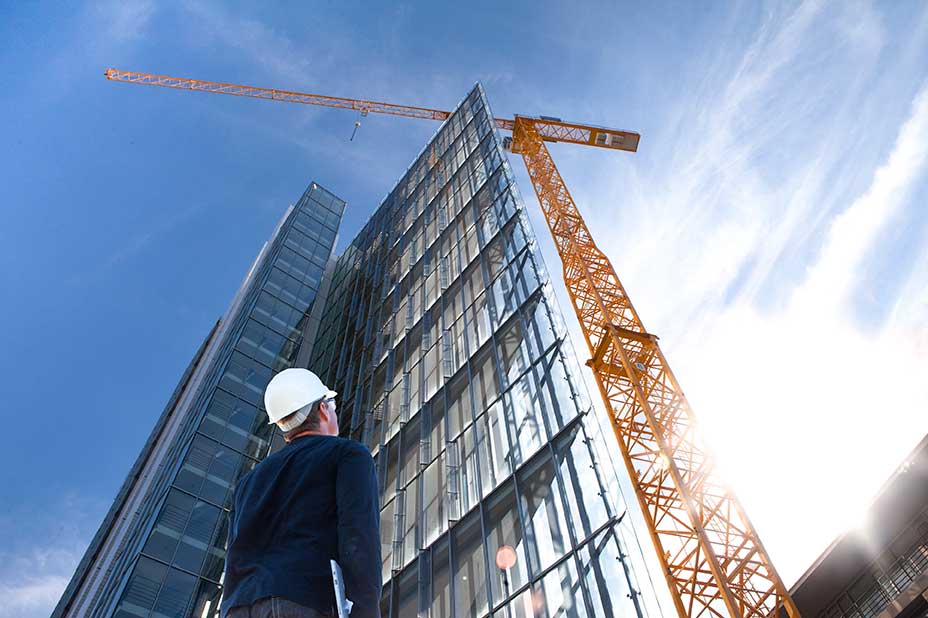
Virtually all crane owners understand the importance of professional maintenance and inspections - after all, both of those things are required by law. Yet it can be easy to overlook the role that you and your crane operators play in ensuring safe, consistent operation. Those who aren't continually vigilant often find themselves dealing with cranes that don't work properly.
To ensure a safe and well working crane, you and your crane operators must be sure to perform daily inspections before and after using your crane. If you would like to learn more about what such a safety check should involve, read on. This article will outline four key aspects of daily crane inspections.
1. Area Inspection
Crane safety involves more than just the crane itself. It also involves ensuring that the area in which the crane will be operated is free from potential safety hazards. Begin your area inspection by ensuring only workers involved in operating the crane are in the area. The fewer people there are, the lower the chances that somebody will be unintentionally hurt during crane operation.
Next, visually inspect the area to ensure that the crane's load will be able to travel along its course freely. There should be no obstacles in its pathway. There must be an appropriate amount of clearance in both the area where the load will be picked up and the area where it will be placed.
2. Equipment Inspection
Now you may move on to inspect the various physical components of the crane itself. Your goal involves ensuring that none of the crane's parts have become loose, broken, or otherwise damaged. Be sure to give a thorough visual inspection to all aspects of the crane, including the bridge, hoist, runway, and trolley.
3. Wire Rope Inspection
The wire rope represents the single most important component of a crane, being responsible for supporting the load. Begin your wire rope inspection by taking a close look at the rope's reeving. The rope should be seated properly in the center of any drum grooves it passes through. Likewise, there should be no twisting of the wires as they enter the bottom block.
Now take a walk around the bottom block, paying close attention to the wire. Look for any areas where the wire's diameter seems reduced. A diameter reduction often indicates stretching, which can greatly reduce the wire rope's strength. Also look for any of the following problems: broken wire strands, kinking, crushing, and other signs of damage.
4. Operations Inspection
Next, you will want to inspect the buttons and switches responsible for the operation of the crane. Make sure that the main pushbutton remains off while you perform these tests; you don't want the crane to respond to any of your button pressing.
Push down each of the operations buttons in turn. They should move smoothly through their full range of motion, with no sticking or drag. As you release the button, it should snap quickly pack up to its undepressed position.
Next, you will perform a series of tests with the main pushbutton on. First, test the crane's warning device for proper operation. Now, test that the hoist hook rises as it should when you move the control button to its up position. Test each of the buttons in this manner to ensure that the crane can move properly in every way.
Crane ownership requires great responsibility. Daily inspections are an important part of ensuring that your crane remains a safe and effective part of your tool arsenal. For more information about what it takes to keep a crane properly maintained, please don't hesitate to contact our overhead crane
e xperts
at Advanced Crane Services.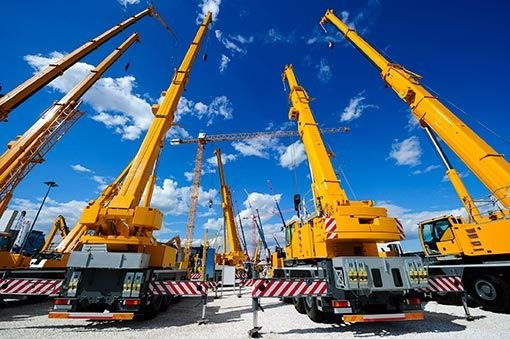
Those managing industrial and manufacturing facilities need to stay on top of load testing needs for overhead cranes. A variety of factors make load testing important when it comes to both safety and productivity around a facility.
Being aware of what makes load testing important can help managers to optimize and take the best possible advantage of testing procedures. The following are six things to know about the importance of load testing overhead cranes:
1. Requirements from OSHA
Perhaps the most important thing anyone in charge of a facility using overhead cranes needs to know is that load testing is mandatory on overhead cranes according to the Occupational Safety and Health Administration (OSHA).
OHSA stipulates three different types of inspection must be performed on overhead crane equipment.
First, an initial inspection must be performed on new equipment. Frequent inspections should be carried out on a monthly or daily basis depending on the service class of the equipment in question. Periodic inspections are another type of inspection that needs to be carried out annually, semi-annually, or quarterly depending on service class.
2. Prevents Emergencies
Load testing is aimed at preventing emergencies and resulting injuries. Without load testing, crane users will be unaware of developing malfunctions until it is too late.
Cranes are expected to support heavy loads on a regular basis. Naturally, wear and tear will occur on the parts that make up cranes and hoists. Load testing required by OSHA is designed to pinpoint any functionality issues that could create hazards and cause worksite injuries if they are not addressed and corrected.
3. Discovers Bottlenecks and Other Problems
However, preventing injuries is not the only benefit of load testing. Load testing can give personnel at industrial and manufacturing facilities important insight into how crane equipment is working and what potential bottlenecks are occurring during regular operations.
The process of carrying out load testing can determine which issues are causing the loading of equipment to take longer than it should. In addition, testing can show any weaknesses in the performance of overhead crane equipment that could require repairs or make it advantageous to purchase new equipment pieces to fix the issue.
4. Increases Productivity
The discoveries made during load testing can allow managers to implement changes that make facilities more productive.
Certain functional errors in crane equipment might only become apparent during the stressing performed during load testing. However, they can be repaired to make the process of using overhead crane equipment more efficient and productive.
Productivity improvements can improve the bottom line of an industrial or manufacturing operation over time.
5. Allows for Maintenance of Overhead Crane Equipment
Load testing can give managers an opportunity to include the necessary maintenance procedures into the schedule.
During load testing, you can set aside time to observe and analyze the functioning and performance of cranes. This is a good opportunity to ensure that all routine maintenance is carried out carefully and adequately.
6. Increases Familiarity with Crane Processes
Carrying out load testing can be good for personnel. The processes involved can leave personnel better informed on crane parts and operations. This can lead to better operators who are more efficiently able to execute tasks using crane equipment.
An official load tester can be designated to handle the responsibility when it comes to more involved periodic or initial inspections. However, personnel can share responsibilities when it comes to handling frequent inspections so that they can be trained about crane parts and maintenance.
If you need assistance with organizing load testing for overhead cranes and hoist equipment used at your facility, you can consult our experts at Advanced Crane Services. At Advanced Crane Services, we offer inspection and testing services for overhead cranes used in a wide variety of different types of industrial and manufacturing facilities.
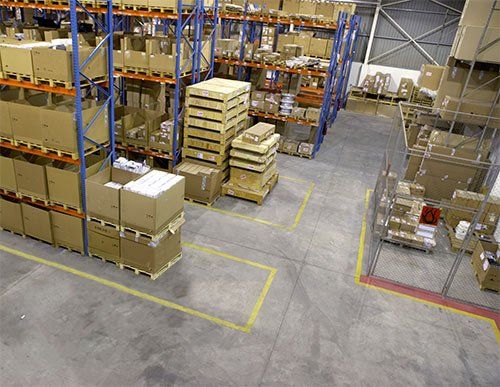
On April 4, 2017, the Occupational Safety and Health Administration (OSHA) reported that a worker in Katy, Texas, had been crushed between a bulldozer and a storage container. Sadly, tragedies like this can happen in any workplace if certain precautions aren't taken. If your business has a warehouse or works with any type of hazardous equipment, here are just a few things that you should be doing.